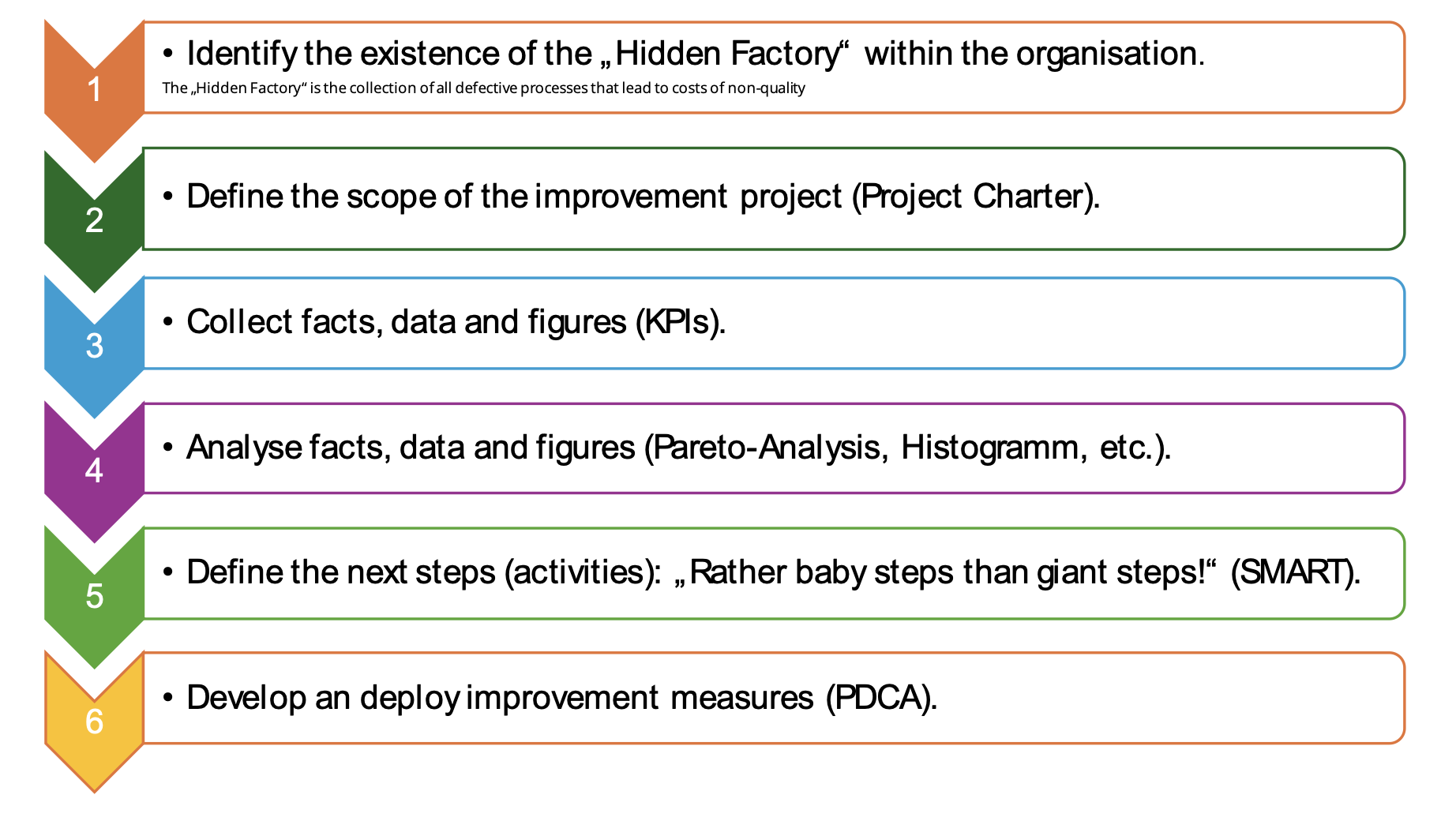
Philipp Rosenthal
This picture was taken in Japan.
Japan has been one of the world's leading economic powers for decades. Japan is an island without own natural resources. It highly depends on the import of almost all raw materials and on a successful export business. The Japanese island regularly suffers from the consequences of natural disasters. And despite everything, Japan has been steadily among the top 3 world economic powers since the end of World War II.
How is this possible?
Japanese companies and the Japanese people know that producing high-quality products and services at an acceptable price is a matter of survival. It is part of the Japanese culture to never be satisfied with the status quo: processes are continuously reviewed and improved. The system is constantly being questioned, optimised, adapted and adjusted, step by step, little by little. Japanese companies are so successful because they "never stop improving."
What can we learn from this?
The facts and figures mentionned on this website are issued from the literature.
The list of the references can be found under "Impressum"
Did you know, for example, that a department manager in Western companies spends about 60% of her/his working time specifically on trouble shooting (1)? A division manager invests about 30% of her/his working time in solving recurring problems(2). Job descriptions often do not include these activities that go "under the radar." Unfortunately, this 30 to 60% of your working time does not add any value. Neither to your organization nor to yourself.
Are you aware that in 94% of the problems that arise within an organisation, the collaborators have no influence whatsoever (2), because the causes of these problems are deeply rooted in the processes or the system?
The consistent implementation of the TQM approach can bring 20 to 25% of an organisation's annual turnover as savings. In the first 12 to 18 months, the cost of non-quality can be even reduced by 50% (3).
It's "a lot of money for free!" as Philip Crosby used to say.
Especially in times when raw material and energy prices are rising, and the shortage of skilled workers has become a reality, companies must pay even more attention to their resources.
At QUALITY CHEQ, we are TQM experts. With our know-how and expertise, we accompany you on the path to sustainable success.
If the Japanese can do it, so can we!
info@quality-cheq.com
+49-(0)421-16 17 43 05